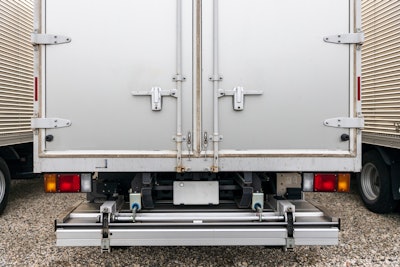
Since the pandemic days, Less-than-Truckload (LTL) offerings are everywhere. As companies strive to optimize supply chains and reduce costs, LTL shipping has won popularity in freight with emerging trends in the practice following suit. But with all growth comes a unique set of challenges, and LTL is no different.
Larissa Franklin, packaging development manager at National Motor Freight Traffic Association, Inc. (NMFTA), says LTL freight handling is different than most and can be rough because shipments are consolidated with others, leading to multiple transfers and increased handling.
"As these smaller shipments are loaded and unloaded at various terminals along the way, the risk of damage rises due to frequent movement and varying handling practices. The shared nature of LTL freight also means that packages are often stacked and maneuvered to maximize space, which can further subject them to rough treatment. This extensive handling and consolidation process, while cost-effective, can result in a less gentle journey for the freight. However, there are ways to mitigate potential damage to freight," says Franklin.
The first step is in the hands of the shippers. Shippers should ensure their freight is properly packaged. This includes understanding their products’ minimum packaging requirements, explains Franklin, and adhering to the Packaging Rules set forth in the National Motor Freight Classification (NMFC®). By complying with the stipulations set forth in the NMFC, shippers can likely mitigate the risk of damage.
"Proper blocking (Blocking involves placing wooden or metal blocks around freight) and bracing are also important. Blocking and bracing, either with dunnage or other freight, prevents handling units from shifting significantly during transit," says Franklin. "While being transported on the road, there are intense vibrations and shock that freight must endure, and by preventing as much movement as possible, the chance of damage also decreases. Often, forklifts and other mechanical handling equipment are necessary to move the freight around docks and into and out of the trailers. Ensuring that packaging can facilitate mechanical handling is important."
One potential example could be by way of using 4-way entry pallets to provide easy access for forklift tines and reduce the risk of punctures to the packaging— which in turn could damage the freight.
Best practices in packaging come from those thoughtful considerations. Franklin explains, shippers should make a checklist with these 3 elements:
- Proper and clear labeling
- Marking
- Potentially placarding
"Having large legible labels that conspicuously display address and contact information will help mitigate loss of handling units, and pictorial markings will help communicate any special handling and/or stowing instructions for carrier personnel. Another way to reduce the chance of lost cargo would be to ensure that handling units are properly unitized, meaning that there is sufficient shrink or stretch wrap and/or banding to secure the load," says Franklin.
In the end, LTL carriers are selling space, which is why density is an important part of a carrier's costing model. Although NMFTA does not consider any economic factors or rates when amending the NMFC, it is understood that density plays an important role in charges. The ability to “max out” the weight and “cube out” the area of the trailer, Franklin explains, will help the carriers increase efficiency and reduce costs. If shippers minimize their footprint on a trailer as much as possible, then they will likely be helping in this endeavor.
LTL has its limitations but plenty of room for improvement. "By working together, shippers and carriers can optimize packaging and transit activities to reduce unnecessary waste from damaged products and ensure cost savings for both parties," says Franklin, and that efficiency is, after all, what every business is after.