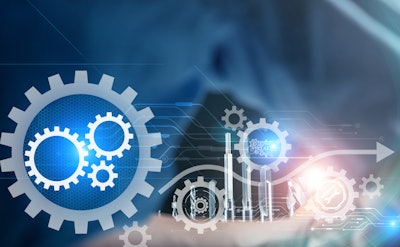
Manufacturers of all sizes have the following three things in common: a talent shortage and widening skills gap, challenges with maintaining the accuracy of their data, and the need for complete transparency throughout their supply chain.
The talent shortage is the most pressing issue. According to a recent report from Deloitte and the Manufacturing Institute, manufacturers could need as many as 3.8 million new workers by 2033. Roughly 1.9 millions of those jobs could go unfilled if current labor gaps remain unsolved. Technology can help close some of those labor gaps while improving data accuracy and transparency. Arguably, the next generation of talent is more likely to be attracted to employers offering an opportunity to work with the most current technologies, not the traditional platforms and solutions put in place decades ago. That’s not to say it is time to abandon investments in legacy systems; rather, it is time to consider the overall impact of all investments in technology.
Mitigating the risks around talent/skills, data, and transparency for manufacturers requires a rethinking of the traditional digital transformation mindset, focusing on a library of smarter tools and specialized technology applications, but within a single platform. In doing so, they can quickly realize the promised benefits, like more productive teams, stronger customer relationships, and tighter collaboration throughout the supply chain, without the headaches and frustration of disconnected systems and limited “solutions” that only solve one problem.
The Downside of Digital Transformation
The emerging lesson of the last decade or so of digital transformation is that, as teams and organizations acquire more digital tools, those tools create information silos where critical data is managed in only that tool, or a platform supports only a few parts of the organization. Meanwhile, it’s still common to see a mix of digital tools along with traditional spreadsheets, paper forms and whiteboarding.
It’s those information silos and their data inconsistencies that erode the gains of investing in digital transformation. Disconnected siloes, online and offline, make it difficult to get a big picture view of what is happening across the company and the supply chain. For example, pulling a production report, tracking KPIs, or getting ahead of potential delays is not a straightforward process. It requires employees to sift through information located in spreadsheets, ERP, PLM, digital tools, etc.
Given these factors, it is no wonder a recent productivity survey of 2,000 workers found 39% of workers say their manual work has increased compared to a year ago. In fact, they are spending 11 hours or more combining through data sources just to do their job, keeping them from working on meaningful tasks and projects that add value. This lost productivity and impact is due to Gray Work, the time and resources wasted when the combination of ad-hoc processes and disconnected systems and technology make it more difficult to track down data and information.
Beyond day-to-day productivity losses, inconsistent data makes it difficult for a manufacturer to make strategic decisions, spot trends and get ahead of potential issues, allocate proper resources, and ensure timely equipment maintenance. Further, it holds a manufacturer back from easily transferring knowledge to employees and the next generation of manufacturing professionals.
The Ripple Effect of Bad Data on the Supply Chain
Inaccurate or inconsistent data can also wreak havoc on the supply chain. Here is a classic example when introducing a new safety protocol on the shop floor. A new process is literally written on a white board and rolled out to the floor to manage. Since the process impacts several teams and plants, it must be rekeyed into multiple systems.
The next day, the whiteboard is erased, but the manual input was not 100% accurate. When that new protocol goes live, workers make mistakes leading to delays at best, and, at worst, accidents. In turn, these delays slow down production, putting unnecessary burdens on supply chain partners as the issue cascades through multiple manufacturing plants.
Now, with the advent of AI, the stakes for accurate data are even higher. Manufacturers are cautiously optimistic about AI. That same productivity survey found 92% are curious about AI-powered tools that can potentially enhance productivity and efficiency. Yet 94% are concerned about the risks of AI when it comes to data security, compliance, and privacy.
How Manufacturers Balance Data Accuracy and AI
Over the past several months, I’ve spoken with manufacturers in automotive, shop floor management and materials handling. Here are three ways they manage data while reducing Gray Work and wading into AI:
- Supporting autonomy without compromising data accuracy: Recognizing that teams have preferences for digital tools, you can strike a balance in keeping what works while not creating shadow IT or technology and app sprawl. It is not the tools that matter as much as it is the ability to easily access information across the company. You can address this using a dynamic work management platform combining a library of pre-built solutions for the most common challenges and use cases and high levels of customization for your processes and workflows.
- Encourage workers to improve processes: Nobody knows a job better than a person who is doing it every day. They are more likely to come up with smart shortcuts that benefit their team and others in the company. This is why low/no code development has taken off. Encourage them to create and share new forms and apps. With the safety net of a work management platform, innovative ideas can be quickly approved and become part of the workflow. You might even see the much-anticipated disappearance of all those spreadsheets and paper forms.
- Start small with AI: It is easy for anybody to dive into AI, and odds are, your employees already have started using it in small instances such as emails or marketing content. If you haven’t already, now would be a good time to institute an AI policy. This way, you can get ahead of any AI hallucinations before they seep into business processes and workflows. When it comes to starting with AI, begin with a small, controlled set of data and users. Choose simple workflows where you already know the outcomes so you can benchmark progress and accuracy.
While manufacturers have many challenges in common, what separates the fastest-growing ones is an ability to see the road ahead and align people, processes and systems against their goals and anticipated challenges. Only then can you build your foundation for success, empowered by the confidence of accurate, consistent data to guide decision-making throughout the organization.