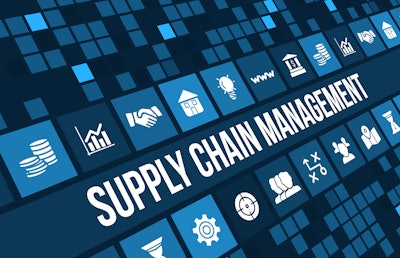
Supply chain planning encompasses a broad range of processes and activities, all of which are closely tied to the success of an organization’s supply chain. From developing production and materials strategies to managing demand, creating a master production schedule, and more, there are a lot of moving parts that supply chain leaders need to account for in their planning—and plenty that could go wrong along the way.
Drawing from data collected in late 2024, this article breaks down the cost of supply chain planning and focuses on two specific processes that can drive costs higher if they are not effectively managed: Creating and managing the master production schedule and managing demand for products. After discussing some of the most common obstacles to cost efficiency in these processes, here are four strategies that leading supply chain organizations use to manage their planning costs.
Breaking down the total cost of supply chain planning
Cost measures are an effective way to evaluate efficiency in planning. The total cost of supply chain planning includes personnel, systems, overhead, and other costs for both internal resources (those within the enterprise or parent organization) and external or outsourced resources (such as third-party organizations) that perform any part of this group of processes.
Figure 1 shows data on supply chain planning costs from 462 global respondents. In this specific measure, cost is normalized (or divided) by revenue per $1,000. This enables organizations to benchmark their performance against peers and competitors regardless of organizational size.
APQC
There is a sizeable gap in performance between organizations when it comes to the cost of supply chain planning. While organizations at the 75th percentile spend $8.10 per $1,000 revenue on supply chain planning, top performers on this measure (those at the 25th percentile) spend less than a third of that to carry out the same set of processes.
Factors like size, industry, and global location(s) can all play a role in shaping what an organization spends on supply chain planning. While these factors may account for some of the differences in spending between the 25th and 75th percentiles, it’s also true that some organizations spend less because they perform better and are more efficient across multiple areas. Moving from bottom-performer to top-performer status on this measure represents potential cost savings of $11.2 million dollars for an organization with $2 billion in annual revenue.
Process level costs
Figure 2 shows the median (or midpoint, 50th percentile) cost per $1,000 revenue for each of the eight processes that are included in supply chain planning.
APQC
Keep an eye on these two processes to manage costs
As Figure 2 illustrates, creating and managing the master production schedule and managing demand for products are the highest-cost processes for supply chain planning. Driving greater cost efficiency for both of these processes is an effective way to manage costs for supply chain planning as a whole.
A master production schedule (MPS) uses supply data, demand data, and forecasts to determine what products an organization should manufacture, how many (or in what volume) they should produce, and when. An effective MPS helps organizations achieve their production objectives while reducing inventory costs, shrinking lead times, and increasing customer satisfaction.
Managing demand for products is a closely related process that provides critical inputs for the creation and management of an MPS. It includes developing a baseline demand forecast, monitoring activity against that forecast and revising as needed, evaluating and revising the demand forecasting approach, and measuring demand forecast accuracy, among other activities.
Common cost drivers
While these are different processes, they share similar inputs—as well as common bottlenecks and inefficiencies. For example:
» A lack of collaboration and communication (both internally across business functions and externally with supply chain partners) makes it harder to gather important data for these processes.
» A high degree of inaccuracy in demand forecasting (which is challenging during disruptions and chaos) will require organizations to revise their forecasting methods as well as the MPS.
» Highly manual approaches to gathering data and forecasting (for example, the manual use and analysis of spreadsheets) will cause the process to take longer and increase the risk for inaccuracy.
» Equipment downtimes or other mechanical problems can disrupt production targets and require revised planning and forecasting.
4 effective strategies for managing supply chain planning costs
To avoid or mitigate challenges like these:
» Deepen communication and collaboration with sales and other internal groups to get a more accurate sense of demand. Leading organizations leverage robust sales and operations planning (S&OP) or integrated business planning processes to ensure all key stakeholders are engaged.
» Build collaborative ecosystems with external partners that protect sensitive data while sharing information and knowledge. While this can be challenging, many organizations are already using such ecosystems to sharpen their planning and drive innovation.
» Leverage technology. Advanced tools to automate demand forecasting, scheduling, and rough cut capacity planning are now widely available. Used in conjunction with internet of things (IoT) sensors, these tools can automatically adjust the MPS based on real time changes in the environment like supplier disruptions or equipment downtimes.
» Continuously improve your planning processes. For example, benchmark and work to improve on-time delivery rates, inventory accuracy, production efficiency, customer satisfaction, and other KPIs related to the broader supply chain planning process.