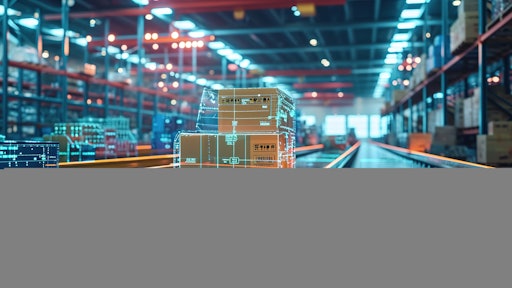
The effects of unexpected events such as a natural disaster or a worldwide pandemic have far-reaching and long-lasting implications for manufacturers. Whether global or local, supply chains and manufacturers feel the strain long after an event is over. Lingering disruptions take the form of extended lead times, rising costs, and logistical bottlenecks. In a time where cost control is more critical than ever, manufacturers must mitigate potential increases in material costs and build supply chains that are not only resilient but adaptable to inevitable future disruptions.
According to BCI’s Supply Chain Resilience Report, top concerns manufacturers face over the next five years include cyber-attacks or data breaches, adverse weather conditions, and natural disasters, all of which pose significant risks to supply chain stability. Energy scarcity and new laws or regulations also rank high on the list, reflecting the diverse and unpredictable nature of challenges manufacturers must be ready to address. This broad spectrum of concerns underscores the complex nature of managing a modern supply chain.
Fortunately, there is reason for optimism. Manufacturers have a powerful ally, a capable tool in their toolbelt, which comes in the form of artificial intelligence (AI). To be clear, AI in manufacturing isn’t new. Since the 1960s, manufacturers have utilized different forms of AI for basic automation—handling repetitive and time-intensive tasks. Over time, applications have evolved, moving beyond basic automation to sophisticated systems that enhance decision-making, productivity, and efficiency. As we move into 2025, manufacturers are leveraging AI to predict disruptions, optimize processes, and improve overall performance. In the year ahead, AI’s influence in manufacturing will continue to grow, offering solutions tailored to modern challenges. By leveraging AI, manufacturers can proactively address supply chain challenges and maintain a competitive edge.
Predicting the unpredictable
When it comes to managing the unpredictable nature of AI, time and accuracy are crucial; and the evolving technology has proven its ability to detect and even prevent supply chain disruptions before they cause challenges. The time saved allows manufacturers to adjust production schedules, inventory levels, and vendor orders well before issues escalate. A key element to predicting with accuracy is visibility, and when it comes to that clarity, a study by Capgemini found that AI-enabled visibility solutions boosted transparency and increased operational efficiency by 22%. Moreover, according to a recent Accenture report, generative AI can potentially reduce supply chain forecasting errors by up to 30%, significantly improving efficiency and resilience across operations. With AI, manufacturers can shift from reactive to proactive strategies, ensuring strength amid disruptions.
Strengthening the chain: building resilience with AI
The benefits of AI aren’t limited to individual operations—they extend across the entire supply chain. AI improves vendor collaboration by analyzing vendor performance and reliability, helping manufacturers optimize relationships and build stronger partnerships. AI-enabled platforms provide end-to-end visibility into the supply chain, from raw material sourcing to final product delivery.
AI also plays a crucial role in improving internal operations. Predictive maintenance systems, powered by AI, leverages machine learning algorithms to analyze real-time sensor data, identifying signs of wear or performance degradation. This allows manufacturers to schedule maintenance proactively, avoiding costly downtime and reducing workplace risks. For instance, a production line equipped with AI sensors can predict potential equipment failures, enabling maintenance to be conducted during planned downtimes for minimal disruption. Similarly, AI enhances quality control by using computer vision and machine learning. These systems inspect products with greater speed and precision than the human eye, detecting defects, deviations, or anomalies in real-time. This ensures higher product quality, significantly reduces waste, and strengthens overall resilience and efficiency of the supply chain.
Risk assessment further benefits from AI. Predictive models help manufacturers identify vulnerabilities and mitigate risks before they impact operations. For instance, incorporating a vendor portal that enables seamless communication and data sharing with suppliers can foster trust and transparency, paving the way for long-term resilience and adaptability. These tools collectively create a robust framework for manufacturers to withstand disruptions and maintain operational continuity.
How manufacturers can embrace AI
As AI reshapes the manufacturing landscape, manufacturers must take proactive steps toward digital transformation. To begin, manufacturers should assess their current technology infrastructure, ensuring they have cloud capabilities and robust ERP systems in place, as these are critical for leveraging AI effectively. Investments in data analysis tools and expertise are also essential since AI thrives on accurate and comprehensive data.
Integrating AI into existing systems is another crucial step. Many ERP platforms now offer AI integrations, providing features like predictive analytics and real-time reporting. These integrations create a seamless flow of information across the organization, enhancing decision-making and operational efficiency. Finally, manufacturers can build stronger vendor relationships through tools like vendor portals, ensuring their suppliers align with organizational goals and are prepared to adapt to changes.
AI - A catalyst for resilience
AI is far from a futuristic concept—it’s a practical tool that’s transforming discrete manufacturing today. From predicting supply chain disruptions to enhancing operational efficiency, AI empowers manufacturers to navigate challenges with confidence and agility. By integrating AI into their operations, manufacturers can build resilient, adaptable supply chains that thrive in an ever-changing world. The journey requires investment and diligent effort, but the payoff is clear: a stronger, smarter manufacturing operation that’s ready to face whatever the future holds.