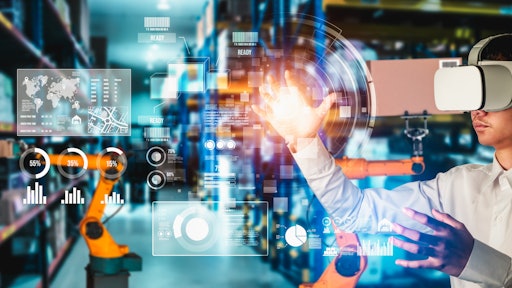
If we’ve learned anything from the launch of Apple’s Vision Pro headset, it’s that we’re on the verge of a whole new wearable-computing future. And while some people may choose Apple’s goggle-style headset, very soon others will opt for the emerging category of smart, augmented reality (AR) glasses. Some, of course, can choose both.
Although headsets may transport wearers to a virtual world, AR glasses keep them comfortably engaged in this one, while simultaneously overlaying data and visuals to enhance their lives, jobs, and more. They’re lightweight, more fashionable, affordable, and increasingly innovative.
The supply chains needed to enable mass adoption of AR glasses are already in place, though differences in manufacturing have an important impact on the quality of the AR experience. Understanding these divergent paths is important.
Waveguides Fuel the Rise of AR Glasses
AR glasses, which project digital content into a wearer’s line of sight, have already begun selling. Research firm IDC expects shipments of AR glasses to grow nearly 100 percent over the next few years. Big tech companies and major brands have introduced AR glasses that can connect wirelessly to your smartphone, display content, capture video, and even take voice commands. In fact, depending on the manufacturing process, AR lenses can be fused with prescription eyewear so that millions of people who need vision correction can enjoy clear sight and digital content at the same time.
For manufacturers, much of what goes into a pair of AR glasses are commodity electronics – batteries, projectors, micro speakers and processors. These are well-known components with established supply chains.
What differentiates AR glasses from other consumer products is a component called a waveguide, which is a thin, specially designed lens that allows wearers to see the real world as digital information is projected before their eyes. For AR glasses to become a popular consumer product, waveguide manufacturing needs to keep up. Fortunately, it can.
Waveguides act as a medium on which the content is displayed from tiny projectors on the side of the glasses. There are two main types of waveguides, each with its own processes and path to mass production. Many early AR glasses use diffractive waveguides, which adds a layer of diffractive grating to the glass surface to create images from the projected light. Others have begun to integrate reflective (or geometric) waveguides, which consist of tiny, partially reflective mirrors, embedded in the glass. And while the precision manufacturing of reflective waveguides is innovative, the notion of using glass and mirrors to cast images has been around for hundreds of years.
Reflective Waveguides Improve the AR Experience
Reflective waveguides allow light to exit the projector (which can be any type of micro projector – LCoS, OLED, etc.) then enter the waveguide’s mirrors, where it’s expanded along both X and Y axes and relayed to the wearer’s eyes. This type of mirror-based AR projection results in bright, true-to-natural-color images within a wide field of view. Light is more simply and precisely directed to the eye to display information, rather than leaking out from the glasses and indicating to others that the wearer is looking at something they can’t see.
What’s more, reflective waveguides are easier on batteries, so the AR glasses run much longer between charges – a key requirement if AR glasses are to truly attract consumers.
Scaling Up Manufacturing of Reflective Waveguides
Having established the high quality and performance of reflective waveguides, scaling up manufacturing has been the next step. Fortunately, because working in glass is as old as mass manufacturing itself, the processes already existed to precisely coat, stack, slice, polish and shape reflective waveguides for widespread assembly into AR glasses.
Unlike much of today’s consumer electronics manufacturing, producing reflective waveguides doesn’t require semiconductor-level cleanrooms and other processes to achieve high yields. It does, however, require standard glass processing tools, machinery and materials. Therefore, in ramping up production of reflective waveguides, it’s been important to partner with leading glass companies, as well as advanced electronics manufacturers, to develop a powerful supply chain.
Now, with the manufacturing supply chains in place to produce millions of reflective waveguides, consumers everywhere will soon begin to enjoy AR experiences in their daily lives. No heavy headset needed.