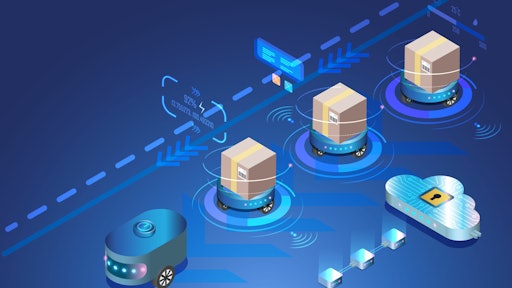
The collaborative use of mobile robotics has the potential to revolutionize case-picking applications, boosting efficiency through route optimization, teamwork with human pickers and error reduction.
In the intricate web of the U.S. supply chain, where millions of products are constantly on the move, the efficiency of operations is paramount. One critical aspect of this efficiency is the process of case picking, a fundamental operation in warehousing that involves selecting products in full case or carton quantities to fulfill customer orders. In recent years, the spotlight has turned towards automated collaborative case picking as a game-changer in enhancing efficiency.
The Role of Case Picking in Warehousing
Cases play a crucial role in the U.S. supply chain. They facilitate efficient handling during transportation and storage, ensuring that products remain protected, and logistics streamlined. Retailers commonly receive products in cases, breaking them down into individual items for sale.
This process allows for a seamless and organized flow of goods through the supply chain. Case picking is a fundamental warehouse operation, particularly in distribution centers (DCs) serving retail stores and e-commerce platforms. It involves selecting products in full case or carton quantities to fulfill customer orders efficiently. Unlike picking individual items, case picking is designed to streamline the process for bulk orders. Pickers navigate through various storage mediums, including pallets, carton flow and shelving, to select the required cases.
Challenges of Manual Case Picking
Manual case picking, the prevalent method in the industry, involves a picker walking through warehouse aisles with a pick list and a hand jack. The picker manually selects one or more full cases, stacks them and organizes them for further packing and shipping. This process, however, is labor-intensive and prone to inefficiencies.
The warehousing industry grapples with labor shortages, and the time-consuming nature of case picking exacerbates the problem. With manual case picking comprising approximately 55% of a warehouse's total labor, the industry faces difficulties in finding and retaining skilled workers. Moreover, the risk of injuries during the manual case picking process adds to operational challenges and costs.
According to Warehouse & Distribution Science, warehouse case pickers spend 55% of their time to traveling, 15% to searching, 10% to extracting, and 20% to paperwork and other activities. Upon analyzing this breakdown, collaborative mobile robots effectively eliminate a significant portion of the time spent on travel, searching and paperwork by associates. This enables them to focus more on higher-skilled tasks, leading to a substantial increase in the efficiency and speed of case picking.
The Opportunity for Efficiency Gains through Automation
The opportunity to reduce time spent on manual case picking lies in addressing the associated challenges, particularly in travel, searching, and paperwork. Collaborative mobile robotics emerge as a transformative solution to streamline these operations, optimize travel routes and enhance overall efficiency.
1. Efficient Routing and Navigation:
Advanced algorithms consider item locations, traffic patterns and obstacles to choose optimal paths enabling zone picking. Unnecessary detours and congestion are avoided, significantly reducing travel time for both robots and human associates.
2. Collaboration with Human Pickers:
Collaborative mobile robots or Autonomous Mobile Robots (AMRs) collaborate seamlessly with human order pickers. The AMR meets the picker at a designated picking position, loads the item and autonomously transports it to the offload point. This collaborative approach ensures efficient item retrieval without unnecessary waiting time. Mobile Robots, significantly reduce searching time for associates through collaborative work, efficient picking processes, optimal resource allocation, scalability and improved warehouse layout.
3. Free-Floating Policy:
Unlike fixed assignments, AMRs operate under a free-floating policy. They dynamically assist wherever needed, responding swiftly to changing demands and optimizing travel routes.
4. Warehouse Layout Optimization:
Researchers evaluate different warehouse layouts, including traditional and cross-aisled designs. The addition of cross-aisles can reduce travel time by providing shortcuts between picking locations. Simulation models help identify the optimal layout that balances efficiency and cost-effectiveness. Automation of data collection and inventory tracking also reduces paperwork time, minimizing errors and allowing associates to focus on tasks requiring human intervention.
Closing the Gap with Collaborative Robots
For the past 35 years, the case picking method has largely remained unchanged, with manual methods being labor-intensive and fully automated solutions proving inflexible and costly. Collaborative robots are poised to fill this gap by offering a flexible and efficient solution that optimizes operations, reduces labor dependence and enhances overall warehouse productivity.
As the U.S. supply chain continues to evolve, the adoption of automated collaborative case picking powered by mobile robotics becomes a strategic imperative. The efficiency gains realized through reduced travel, searching and paperwork times, coupled with improved safety and operational effectiveness, position this technology as a transformative force in modern warehousing. Embracing the collaborative potential of robotics is not just about increasing efficiency but also about futureproofing the supply chain against labor challenges and operational constraints, ensuring a seamless and agile flow of products through the interconnected nodes of the supply chain.