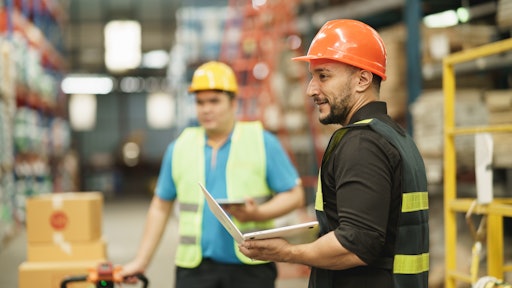
The calendar has turned to 2024, and while it’s a new year, manufacturers continue to grapple with familiar challenges. In Protiviti’s recent survey discussing top risks in the manufacturing and distribution industry, leaders noted economic conditions such as inflationary pressures, as well as uncertainty around core supply chains as top concerns.
An increase in catastrophic events has only complicated matters and driven the continued uncertainty that plagues manufacturing today. Events like geopolitical conflicts and natural disasters lead to severe manufacturing consequences. As the Red Sea crisis continues, shipping volatility has spiked. In 2023, the United States had 28 separate weather and climate disasters costing at least 1 billion dollars; the highest in a calendar year. This unfortunate trend appears unlikely to reverse, as 2023 was the fourth consecutive year in which 18 or more separate billion-dollar disaster events have impacted the United States. This standard is becoming the new normal.
For manufacturers who rely on supply chains and warehouses as integral components of their business, visibility into potential risks or concerns is essential. Never has it been more important to promote transparency across each facet of the supply chain. For the agility and transparency required, pen and paper will no longer cut it, and outdated solutions simply won’t suffice in the face of evolving modern challenges. Adopting and leveraging technology solutions that drive supply chain visibility offers manufacturers a way to steer through turbulent times and succeed in the months and years ahead.
Core Challenges Continue to Evolve
When determining how to bring warehouse visibility to manufacturing organizations, it’s vital to understand the problems which need solving. Inflation, international conflicts, and natural disasters each bring a certain set of challenges to manufacturers. By fully understanding challenges at hand, manufacturers can deploy technology that seeks to solve for each factor contributing to the circumstances.
Inflation
Increasing inflation rates have created soaring costs for raw materials, labor, and essential inputs, squeezing manufacturers' margins. The overall elevation of costs impacts processes and prompts difficult decisions, including whether to raise prices, reduce quality or accept below standard margins to maintain customer satisfaction. Inflation may also disrupt long-term contracts with suppliers due to diminishing payment values. Fluctuating inflation rates create uncertainty in financial planning which makes it even more challenging to predict and manage costs effectively.
International Conflicts
International conflicts pose geopolitical risks, disrupting global trade networks. Tariffs, trade barriers, and export restrictions equate to increased costs for importing essential raw materials. For manufacturers who rely on international suppliers, delays or even the ability to source materials creates significant disruption to production schedules, decreasing on-time-deliveries and impacting customer satisfaction and the overall value chain manufacturers play a key part in. Geopolitical instability can disrupt transportation routes, further impacting the timely movement of goods. Heightened uncertainty and risk from international conflicts may deter investments in expansion or innovation, limiting adaptability to changing market dynamics.
Natural Disasters
Natural disasters physically impact facilities, damaging infrastructure, disrupting transportation and altering power. This can lead to equipment damage, production halts and loss of inventory. Suppliers and distributors in the supply chain may also face challenges, causing delays in raw material delivery. The overall impact for manufacturers includes increased costs, production bottlenecks, and reduced capacity, which present very real challenges in meeting customer demands. With recovery and rebuilding as part of the process, prolonged disruption can lead to diminished operations, cutting into the overall bottom line with unplanned overhead costs.
Each factor contributes to a reduction in warehouse resiliency by introducing uncertainties in the timing, cost, and regulatory aspects of the supply chain. Uncertainties exploit the underlying costs of having little transparency into the supply chain, making it harder for warehouses to maintain optimal inventory levels, plan for contingencies, and ensure smooth operations.
Enterprise Resource Planning Enables Warehousing Visibility
By offering a centralized platform for managing data real-time from supplier partners, analyzing material and inventory information, and making decisions, enterprise resource planning (ERP) solutions empower manufacturers to handle warehousing challenges brought on by industry disruptions. At their core, ERP solutions bring visibility to the supply chain from end to end. Through a comprehensive view of suppliers, transportation logistics, and inventory, manufacturers can identify disruptions quickly, and offer the information required to build sustainable solutions. By incorporating forecasting and planning tools that are driven by market trends and data, manufacturers can more accurately forecast future demand, and adjust their warehousing management approaches accordingly. This ability to be ahead of the disruption game is critical as it enables manufacturers to optimize inventory levels, which helps mitigate inflation-based cost discrepancies and errors in production counts. In the current environment, contingency plans are becoming more important for manufacturers to have at the ready. Fortunately, the increased enablement of risk monitoring allows for alternative sourcing strategies that mitigate effects of disruption.
ERP solutions streamline warehouse processes and enhance overall operational efficiency. Automation features within ERP systems reduce manual errors, increase productivity, and enable warehouses to operate more smoothly, even when faced with external challenges.
Bringing Urgency to Ongoing Struggles
The surge in catastrophic events, coupled with ongoing geopolitical conflicts, underscores the urgency manufacturers must bring to solve supply chain complications. In times of uncertainty, relying on outdated solutions only compounds negative consequences already being felt by the industry. Investing in technologies such as cloud-based ERP solutions that deliver a secure, centralized platform for managing data, analyzing information, and making informed timely decisions, empowers manufacturers to tackle disruptions head-on and anticipate coming challenges. By enhancing supply chain visibility, streamlining processes, and enabling proactive risk management, ERP solutions equip manufacturers with the agility and resilience needed to thrive amidst turbulent times.