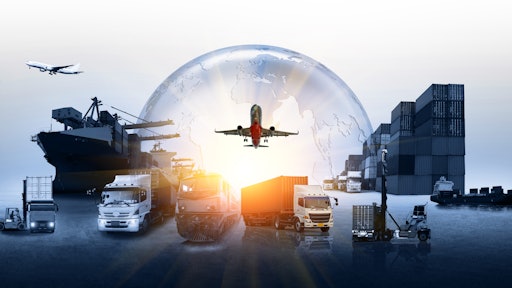
We’ve become used to hearing the term ‘disruptions’. Inside and outside of the supply chain.
Disruptions to travel, to appointments, to daily life. Disruptions to dispatches, to deliveries, to supply chains. Even disruptions to entire businesses.
Since the pandemic, ‘disruptions’ has slipped into public speech as easily as they’ve slipped into everyone’s every day. But what began as delays due to COVID restrictions and outbreaks has since transitioned into semi-regular crises across global trade routes and inside companies.
For end consumers, this causes added frustration, added costs, and added wait times. Enough to roll your eyes about. For businesses and their supply chain superheroes, however, these disruptions are having widespread impact. Impact that’s proving detrimental to teams, operations, and our economy.
Examples Are Everywhere
The Red Sea was the epicenter for disruptions and reroutes at the start of the year. As tensions rose and the region became too volatile for passage, many shipping companies opted to divert from one of the most active trade routes in the world, or even discard operations in the area altogether.
To put the crisis into numbers, the Red Sea accounts for around 12-15% of global trade, 30% of global container traffic, and 8% of LNG, widely used as a fossil fuel alternative. Meaning reroutes had a not insignificant impact worldwide.
The blockage in the Suez Canal was also one of the most talked about events of 2021, and for good reason. We all remember the memes and that tiny digger that tried to free the Ever Given, but the reality underneath that was much starker. Much like the Red Sea, about 12% of trade passes through the Suez and as companies were forced to turn back, it meant adding time, resource and fuel spend onto everyone from the owner to the end consumer.
Russia-Ukraine War, winter storms and adverse weather conditions, Panama Canal drought – like I said, no shortage of examples.
The Global Cost
Lloyd’s List estimated that the Suez Canal incident cost around $9.6bn of goods each day – and it’s likely a similar figure for the Red Sea diversions.
The same goes for insurance premiums. Imagine you crashed your Maserati twice in one week - that’s sort of the equivalent of what we’re looking at here. Prior to the Red Sea attacks, insurance rates were around 0.6% of the value of cargo, but now, they’re around 2%.
These costs aren’t just floating around, they’re having real-life impact on the public. For many of businesses facing supply and demand jeopardy, the only way to tackle the issue is to pass costs along to the end consumer, which many of us see in our grocery bills since the pandemic. Raising alarm bells for oil prices, goods prices, and access to products.
A lesser-discussed effect is the matter of brands’ reputations. The ability to provide the agreed-upon goods, within the agreed-upon timeframe massively influences how a business is perceived. Delays jeopardize that. And we’re not just talking about two or three days, we’re talking weeks or months of unstable, unreliable supply and demand.
And what message does that convey? That the supplier is unreliable.
While it’s true that no one could’ve predicted the attacks in the Red Sea or a ~400-meter ship getting lodged into a canal, businesses are still accountable for their agreements. And unless they’re prepared, each disruption could be a nail in their revenue coffin.
Disruptions Could Increase
Disruptions have always had a degree of inevitability. But the number of these and their effect has accelerated in recent years; for every news story that makes it to our headlines, Supply Chain Managers and Chief Operational Officers handle dozens more on the ground.
There are obvious reasons for this, but it could be chalked up to increased globalization. Trading and economies are now so closely connected that disruption on one end can cause serious ripple effects across all partners within the chain.
Localized conflict, climate change, cyberattacks, inflation and spikes in demand are all growing in frequency and impact. In real terms, this can result in communication siloes and lack of visibility, to data breaches and loss of products, to at-risk labor forces and reputational catastrophe.
For many teams on the ground, the supply chain has felt like one big disruption in recent years. And it’s crippling global overheads, efficiency, productivity and morale. A recent survey found that 77% of mid-sized businesses face persistent supply chain issues, and around 69% of companies report having limited visibility of their entire chain. Keeping Chief Procurement Officers awake at night.
Prepare to Prevent
Not all disruptions were created equal.
There are those we can predict and those we can’t. Those that are global and those that are local. The headline-grabbing and the behind-closed-doors. But there’s always a common denominator: preparation is always possible.
At the very least, using the right digital platforms like enable Supply Chain Managers and Logistics Leads to drastically mitigate the impact of chain disruptions. Enhanced communication capabilities and task management makes information share that much faster, simpler and more productive. And unexpected disruptions can be tackled collectively, rather than in siloes.
At the very most, digitization can prevent disruptions altogether. Say that conflict spikes inflation and a supplier wants to suddenly increase their rates, and you’re at a standstill because of it. Having centralized document management means there’s no debating SoWs or contract terms – the info is immediately accessible, and collaborators are on the same page.
Digital transformation isn’t about the full automization of the supply chain, by the way. Digitization focuses on providing managers and leads with the right level of oversight, giving them the ability to plan through a challenge or crisis before hitting rocky waters. It connects operational touchpoints and reduces admin- and time-heavy tasks, giving teams the space to strategically plan and deliver solutions.
In other words: it’s integrated, intelligent software for humans. Not instead of.
If the past 5 years have proven anything, it’s that investment into supply chain visibility is investment into greater safety, greater protection, and greater preparation. And regardless of whether the worst-case scenario is becoming the subject of a viral meme, or risk to your people and your products, preparing for operational disruptions is only going to become more imperative.